It was a point of frustration for new hires. As they started working at Nova Flex, some would get exasperated with the time it took to go from job training to producing the company’s LED lighting. They had to master various soldering skills — often taking two weeks — before they could put their abilities to work.
The St. Cloud company also made training difficult by trying to teach too much information at once. This slowed down the learning process and delayed new employees’ opportunities to hit the ground running. Nova Flex decided that the time was right to improve its onboarding process.
Company leaders turned to Enterprise Minnesota in 2021 to work with Nova Flex on continuous improvement. First up was value stream mapping to remove waste from its manufacturing operations. Next, they introduced Job Instruction, a Training Within Industry program designed to improve and standardize employee training.
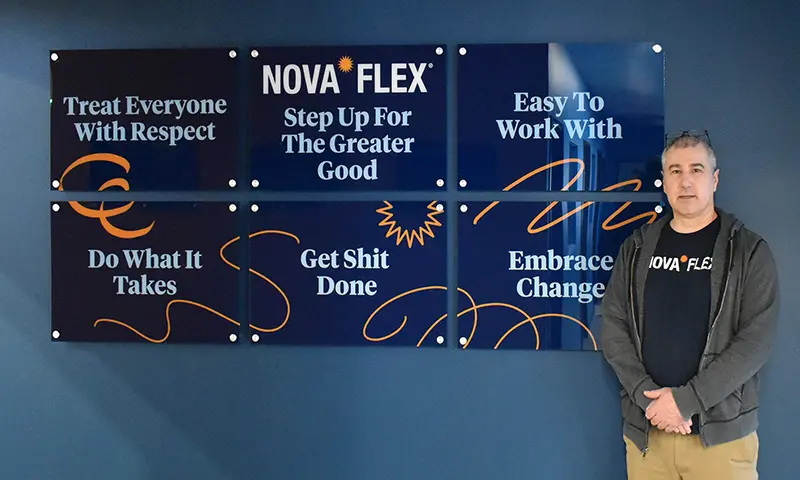
Instead of providing an overwhelming firehose of detail about how to complete a task, Job Instruction teaches trainers to break down a task into understandable steps. These smaller clusters of instruction prevent trainees from getting inundated with information, and it helps them build confidence as they master each step, says Michele Neale, an Enterprise Minnesota business growth consultant who specializes in leadership and talent development. She delivered the Job Instruction program to six Nova Flex employees.
“With Job Instruction, the philosophy is that if the students haven’t learned, the teacher hasn’t taught,” says Dawn Loberg, an Enterprise Minnesota business development consultant. “It’s really about breaking down your processes into actionable items so that the employee can start being productive and adding value and seeing that they are contributing as soon as possible.”
Nova Flex Manufacturing Manager Bob Waline has noticed a major difference since he completed the Job Instruction program with co-workers. First, having the group develop their instructional skills spread training responsibilities among the participants, not just him. It also taught them best practices for effectively teaching employees all the necessary skills. That way, all production staff learn a consistent, unified way to complete tasks no matter who teaches them.
Now, Nova Flex stores each training module in a binder that provides written and visual steps for mastering various skills. The Job Instruction group spent two years creating the training worksheets, meeting weekly to develop and refine the training steps for each task. They started with four or five basic skills and then gradually added training for more intricate work.
The binder includes images, photos, videos, and other material that employees can use to learn new skills or refresh others. Having this resource supports people with different learning styles, Waline says. Previously, there wasn’t an easy way to adjust training to a visual learner versus someone who learns by reading or doing.
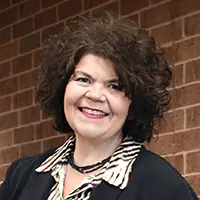
Neale says the cohort that completed Job Instruction transformed the company’s training approach. They incorporated the program’s four-step model to prepare the student, present the operation, try out the performance, and follow up, with the overall objectives to enhance job safety, processes, consistency, and problem solving. “With a little bit of modification in how they train, Nova Flex was able to get that new person adding value in 20 minutes,” she says.
Waline also appreciates that the Job Instruction method holds instructors accountable for the quality and effectiveness of their training. “If they notice a mistake, they stop right there and make sure the training doesn’t continue until the trainee understands what he or she needs to know,” he says. “Before, I think people could give information too quickly and then maybe not notice if the student didn’t have full understanding.”
Now, trainers request feedback, ask clarifying questions of the trainees, or seek a demonstration of the skill to ensure that students understand before going on to the next step, Waline says. Another benefit is that Nova Flex significantly shortened the amount of time it takes to determine whether a new employee is going to be a good fit for a role, says CEO David Kidd.
In addition, trainers benefitted when Nova Flex adopted the Job Instruction approach, too. They gained confidence that they could train others and train them well, where before they generally figured methods out on their own, Waline says. That sometimes led to inconsistency among how production employees did certain steps depending on who trained them. Now everyone is on the same page.
Nova Flex also deployed Job Instruction to cross-train existing employees. Having employees proficient in at least two skills has helped with engagement and retention because staff can work in a variety of operational areas, such as prep, quality control, or shipping, Waline says.
Kidd observes that the work Nova Flex did with Enterprise Minnesota, including the value stream mapping and Job Instruction initiative, has paid off for the manufacturer. “In order for people to succeed, it’s important for us to give clear direction and training. We find that some of the hardest workers and best performers really appreciate the clarity and direction and the knowledge of how to do their jobs well,” he says.
“We found a number of benefits by doing that — creating engagement and productivity from our current workforce as well as when we hire new employees,” Kidd adds. “It more quickly onboards them and gives them insights into the whys of the various parts of their jobs.”
Completing value stream mapping at Nova Flex also improved employee engagement and job satisfaction. The work targeted improving production efficiency from customer orders to cash, removing any bottlenecks or overlapping efforts, says Greg Hunsaker, an Enterprise Minnesota business growth consultant. Fine-tuning processes and redesigning the shop layout to improve flow “were a huge hit with Nova Flex,” he says. “They are still using these methods to look at their processes and find waste. And as they keep removing waste, it makes it easier for them to do their jobs and it results in better quality.”
The entire Nova Flex team has taken all of this continuous improvement work to heart. The effect on employee engagement and retention, and the company’s enhanced ability to grow efficiently, were impressive and palpable during Enterprise Minnesota’s three-year follow-up visit, Loberg says.
“What’s so fun is that now you go in there and everyone is happy, everyone is smiling — it’s such a joyful place to work,” Loberg adds. “It was just an absolute delight to see the growth in the people and the streamlined processes. It’s the commitment from their upper management and the investment in their people that helps them all feel like they are adding value to the output and for their clients while helping the company grow.”
Return to the Spring 2024 issue of Enterprise Minnesota® magazine.