For years, manufacturers have heard that automation can help them meet strategic goals while solving workplace challenges, including filling gaps caused by labor shortages and relieving employees of tedious and physically taxing tasks. While automation offers great promise, its real value doesn’t come simply from installing new technologies, but from combining those advances with strategies that improves processes.
Enterprise Minnesota business growth and continuous improvement experts Eric Blaha and Ally Johnston say the companies with the most success from automation view it as a journey with employee engagement at its core.
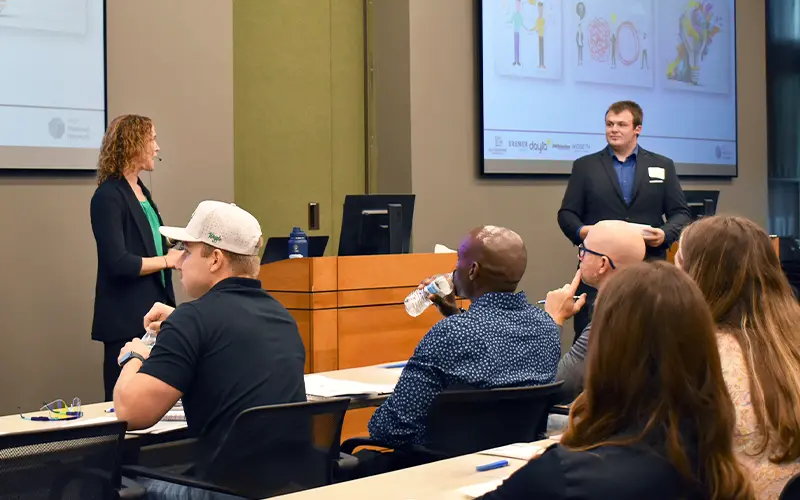
“If we just start automating, we will automate waste and poor processes,” Johnston says. Instead, she and Blaha encourage manufacturers to implement key aspects of lean management, communication, and employee involvement before integrating time- and labor-saving technologies through automation.
The essence of the process they recommend is captured in the acronym VESSA: Value stream, Eliminate waste, Simplify, Standardize, and Automate. The result? The manufacturers they work with boost employee engagement and commitment to the process and identify waste as well as opportunity. When they put automation measures in place, they reap tremendous benefits.
“Going through VESSA gives us the strategy and tools to automate well,” Johnston says. “On paper you go from V to E to S to S to A, but realistically you bounce around. They are all very connected.”
Value stream mapping
Value stream mapping communicates an organization’s future strategy in a way that addresses changing dynamics. It needs to be a live document and regularly reviewed for how well it ties in to where the company is going, its competencies, and its customers. All those things are evolving.
Think of value stream mapping as providing employees with a Waze app instead of a Rand McNally Road Atlas; the destination might remain the same, but during the trip, better ways to reach the goal may surface.
Value stream mapping is a lean tool, but also a mindset and strategy to help organizations continuously evolve, which is critical given today’s manufacturing climate. “Labor’s expectations are a lot higher than they used to be. Employees expect a lot more out of their employment. Customers want productivity improvements and cost reductions; they want partnerships,” Johnston says. Plus, technology is constantly changing, she adds.
Integrating these demands and considerations into a strategy ensures that everyone understands the “why” of the company.
“The ‘why’ isn’t just the mission, vision, and values, but also how employees and the leadership team connect to it,” Johnston says.
With mission, vision, values, and a strategic plan in place, manufacturers can lay out the value stream of where they want to be in the future. That helps drive communication improvements and people’s behaviors. When they’re making decisions day to day, they’re making them in line with the future vision of the company.
Critical to the process, Johnston says, is involving employees in those discussions. “We want the whole organization to understand the value stream, the strategic initiatives, the ‘why,’ because then we’re all pushing in the same direction.”
The ultimate goal is to use lean tools to add value for the customer. Blaha and Johnston advocate teaching employees to see aspects of production as value-add (green), non-value add but necessary (yellow), and waste (red). With those categories identified, automation can drive improvement. “We want those automated robots, CNCs, welders and whatever additional automation we have to add as much value as possible,” Johnston says of the green category.
Yellow represents non-value add, but necessary. These are items like data analytics, putting on PPE, or conducting in-process inspections. Automation can support these as well, with quick pages or vision systems for inspections, for example.
Red, the waste category, includes those activities that take time and resources but add no value, such as looking for misplaced tools or undergoing unplanned maintenance. Lean thinking is critical to identifying wastes in advance of automation. “When we don’t follow processes, when we don’t think about VESSA or this holistic approach to automation, we end up automating waste,” Johnston says.
Eliminating waste
Jumping into automation without identifying waste simply compounds negative results. “Imagine five minutes of waste over 365 days, five years down the road. That’s a lot of time that could have been adding value to the customer and the business,” Johnston says. “Instead, we’re automating that waste.”
Johnston and Blaha urge manufacturers to train and encourage employees to see waste using the green, yellow, and red categories, which improves processes and boosts engagement. “A good day for employees is one where they know they have added value,” Blaha says.
Involving employees also reduces fear, say, about future job loss. Very few manufacturers think of automation as an avenue to reduce their workforce, Blaha says. They may think about it as a tool to reduce labor costs per unit, but the overall goal of automation is often to grow the business or automate the least desirable tasks.
Explaining the objectives of automation and the role employees can play in implementing it is critical. “That allows us to develop trust, which allows us to begin the eliminate waste step by engaging those employees with their ideas and improving upon current processes,” Blaha says.
“If we just start automating, we will automate waste and poor processes.”
Specifically, Blaha recommends simulating automation solutions, brainstorming as a team, and empowering employees to take initiative. He’s also a big fan of “try-storming,” which allows a team to attempt a small change in a controlled environment to see if it solves an issue or improves efficiency.
Try-storming relies on subject matter experts — the employees involved in production — to develop ideas and try them out. “Let’s put together a mock illustration of what this looks like. Let’s do some experimentation, and let’s take away the good and eliminate the bad,” Blaha says.
Boosting engagement through efforts such as try-storming does more than improve automation outcomes. Companies with engaged employees are much more likely to meet their strategic goals and have higher employee satisfaction and retention rates.
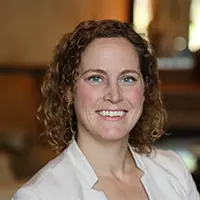
Research shows that just 34% of employees are engaged on the job, Johnston says. When people are engaged, they are more productive, they are more apt to join a committee to improve safety or to suggest ideas, she says. The higher the engagement, the more productive employees are. A key driver of engagement is understanding the lean principles that form the foundation for successful automation.
“So often we hear, ‘We’ve always done it this way’ or ‘this is just how the job is’ or ‘so-and-so trained me, and this is how they do it,’” Johnston says. “We want those phrases to stop.”
Instead, Johnston says, employees should identify operational waste: spending minutes searching for a tool, continuing to get poor quality from a supplier, not having a maintenance plan so a machine is constantly down. “We need employees who are engaged and learning to see because we need those subject matter experts to be suggesting improvements in these areas,” she says.
Simplifying
Johnston points out that often, quality production is kept on track through human intervention — extra steps that aren’t part of the process. “When I hear phrases like Band-Aids, workarounds, adjustments, tweaks, fidgeting, that says they’re doing these things that aren’t standard. They don’t flow and there’s a lot of variation. They have to intervene to make that good part,” Johnston says.
Before implementing automation, manufacturers need to eliminate those extra steps by simplifying, which Blaha says is basically error-proofing processes. He suggests a six-pronged approach to error-proofing: elimination, replacement, prevention, facilitation, detection, and mitigation.
Elimination requires manufacturers to carefully consider where errors originate and eliminate steps that often lead to mistakes. Blaha says a company he worked with recently struggled with a particular part they were machining in two operations. In the first operation, they would drill a locator hole. Then they would move it to the next machining station where they would attach it to that sheet, clamp it, and do the next operation.
But the locating hole wasn’t always perfect, so they redesigned their fixturing and their manufacturing process to eliminate that step. Now they’re machining it in one cell and that part is much more accurate and repeatable. By eliminating that transfer step, they improved the overall quality and productivity because they’re handling the part less.
Replacement involves updating a process with improved technology. Johnston shares an example of a plant inspection process. Replacing the paper checklists and reports with a tablet-based inspection revolutionizes the process.
“I just did an audit where I walked on the floor, took pictures, made auto-generated reports, and boom, that whole thing was replaced with something simple,” Johnston says. “Instead of taking two hours to do a plant inspection, we got it down to 30 minutes,” noting that the instant reporting capabilities of a tablet eliminate potential errors that arise from retyping written notes.
Prevention involves avoiding errors from the outset. Blaha cites the automatic shutoff mechanism on gas pumps that detects when the tank is nearly full to prevent fuel spills. In the manufacturing world, prevention techniques can take many forms.
Blaha helped one client deal with a particularly difficult substance that frequently gummed up the tool used to cut it. The production team looked into different options and found a heat-treated and coated tool that shed the material better.
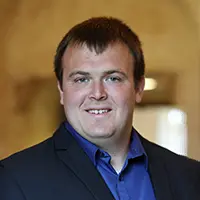
Facilitation allows employees to do the same job, with better guidance. Think of a backup camera on a car, Blaha says. It’s an error-proofing device that facilitates the act of backing up because the camera tells you if anything’s behind you. “It facilitates the operation and allows people to learn it more easily and perform it more effectively with very little training,” Blaha says.
Detection uses technologies to quickly alert employees when something is not right. It might not eliminate the error, but it can limit the consequences when an error occurs. Blaha says tire pressure warning lights on cars are a perfect example. When the light goes on, the driver can pull over before the tire blows out.
Mitigation, the final error-proofing tool, recognizes a mistake is likely or even inevitable, so manufacturers need to take necessary steps to minimize the impact. Blaha likes to share a picture of a foam-filled tire punctured by half a dozen sharp objects. The tire is designed for strength because it is used on heavy equipment in scrap yards; it will get punctured, but the special custom-made tire will mitigate the effects of the damage.
Standardizing
Next in the VESSA process is standardization. It’s critical that the process is repeatable for different employees. That means setting up a very robust process using lean thinking.
Johnston describes working with a client where a group of assemblers was very frustrated with a job that involved welding a certain piece into the equipment to make sure when it swiveled it locked in. “It was a very small space and they felt crammed in. It was just a big struggle,” she says.
To address their concerns, the team started to think about the best person to do that particular job. Then they considered the best sequential order for the process. Next, they thought about the best way to weld it on, opting for the simplest construction. They ended up pushing the “who” and the “when” upstream into the weld process where there were experts in welding, and they had better access to the part because not all the pieces were on the unit yet.
Continuing the lean thinking process, they considered the “why” — and they discovered that when the assembly was sent to their sister company, employees there removed that piece and welded their own. While the solution they developed worked, it didn’t need to.
The lesson: Always ask the “why” first when trying to standardize processes, particularly in advance of automation. “If we just go through the other steps and prepare to automate and then automate the task, we might find out later that it wasn’t necessary,” Johnston says. “That means we’re going to spend a whole lot of time and effort on something that we maybe could have eliminated.”
Automating
The value of the V through S steps of VESSA could stand alone, but adding automation to the mix can lead to exponential gains. With value and waste identified, automation can be implemented to enhance productivity, limit the burden of dull or physically demanding tasks, and streamline the non-value add tasks such as inspections.
As companies adopt automation tools, continued employee engagement is crucial. “You’re not going to do one project and stop engaging those employees,” says Blaha. “We need to share the outcome, share the data, talk to them about what we did, how our productivity changed, how quality changed, how we brought in new business because of this, and really engage them in the final steps of that process.”
Just sharing outcomes isn’t enough, Blaha adds, noting the importance of celebrating with employees and soliciting their feedback. He recommends using some of the ROI gained from automation to invest in facilities — an updated break room for example — to build goodwill in the workforce. He also suggests giving employees an opportunity to share their input on the process.
Johnston agrees that companies need to be intentional about next steps. Manufacturers will generate excess capacity by automating process steps effectively. Filling that capacity so employees feel that increased business coming in will help them continue the automation journey.
Finally, Blaha urges companies to continue encouraging employees to see waste and suggest process improvements. “They know it better than anyone. Keep developing them to be part of the solution,” he says.
Return to the Spring 2024 issue of Enterprise Minnesota® magazine.