When Enterprise Minnesota President and CEO Bob Kill talks to business leaders about lean manufacturing, he hears two common refrains: We tried that once, and it didn’t work. Or they already did a lean project, so they are all set. He finds that many manufacturers share similar misconceptions about what precisely lean is and what it can do for their companies.
There are numerous things Kill wants people to know about lean and how it can help their businesses thrive. Yes, it’s a system for rooting out inefficiency, eliminating waste, and optimizing productivity. But at its core, lean is all about the people in every role at their manufacturing companies. As a strategic initiative, lean harnesses employees’ savvy, inside knowledge, and innovation to make an organization stronger — and one that’s primed for growth.
Successful manufacturers know that lean is not a one-time tactic but an integral and abiding strategic element of their culture.
“When companies say that lean didn’t work for them, we say that a tool is only as good as the craftsman,” Kill says. “When you think of lean as a tool, you leave out the most vital part: the people.”
Employees are both key stakeholders in executing lean and the main beneficiaries. “The more efficient an organization is, the higher the morale and the higher the retention. People feel energized and enabled because decisions get moved through the person closest to the challenge,” Kill says. “Yes, it’s about eliminating waste, but it’s an overall growth strategy that energizes the people.”
Mainly derived from the famed Toyota Production System, lean manufacturing focuses on optimizing processes, eliminating waste, and using fewer resources to create high-quality products. Its chief objective centers around delivering maximum value to customers by focusing on what is absolutely essential to meeting their needs.
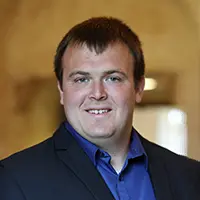
Eric Blaha, a business growth consultant for Enterprise Minnesota, has been involved with lean manufacturing at scores of companies, from global conglomerates to the smallest shops. Seeing diverse companies thrive when they engage in lean work convinced Blaha that it is an effective way to help any manufacturer foster growth. To Blaha, that’s the beauty of lean. Its principles stand up no matter where they are put into action, as long as companies deploy lean as a vehicle for growth, not just a set of tactics or tools.
“A lot of companies focus in on the tactical pieces of lean and think about it as a set of tools they can apply to problems. But the largest and most effective companies in the world think about lean as a strategy for taking its tools and applying them to processes and practices to continue to help them get better,” Blaha says. “Lean is a strategy for engaging employees in real problem-solving, rather than identifying a specific symptom and applying the tools like a treatment.”
There are many ways to approach lean. At its core, though, are several essential foundations that help organizations successfully adopt lean as a strategy. Blaha highlights four:
Workplace Organization – Creating the most efficient, effective, and ergonomically designed workspaces, ranging from a holistic view of an entire operation to individuals’ work areas
Automation – Enhancing flow and reducing waste with the right tools and technology to support operators, such as robotics or vision systems
Process Optimization – Eliminating waste in the manufacturing operation and designing the best way for product to flow through the manufacturing area
Error Proofing – Identifying the most likely places mistakes occur in the process and integrating ways to mitigate these errors and reduce waste
Underpinning these foundational lean elements is a base layer of employee engagement and training. This practice brings everyone along on the journey of continuous improvement. “Companies that really focus on optimizing processes through people development are going to have a higher level of employee satisfaction,” Kill says. “It’s going to drive employee support and retention, and that’s what manufacturers want.”
Blaha notes that many manufacturing businesses get started by artisans or entrepreneurs who developed a new product in their garage. Lean operations were far from their minds as they got established. But as their companies continue to evolve and expand, it becomes vital to take a hard look at embedded processes and existing facilities, he says. By removing steps that don’t add value and energizing employees to share their insight and get involved, leaders can grow manufacturing companies strategically and sustainably.
“Commonly when I do lean projects, there is a light bulb moment where people flip the switch and see the world differently, and that’s really fun,” Blaha says. “It’s a major paradigm shift for manufacturers.”
“I’m training people how to see things differently, not training them in lean,” he adds. “And if you can see things differently, you can solve a lot of problems.”
Read on to see how four Minnesota manufacturers successfully integrate lean foundations in their operations.
WORKPLACE ORGANIZATION
Whirltronics, Inc.
Buffalo
The crowd did not go wild when Buffalo-based Whirltronics began focusing on lean manufacturing in 2003. Employees knew that tackling continuous improvement efforts are no small task, and they were skeptical that the hard work and disruption would be worth it.
Around that time, Whirltronics’ leaders had started learning more about lean and were getting motivated to put some of its principles into action. Inspiration struck for then manufacturing engineer Jennifer Lindquist, who had a vision for optimizing the company’s process for making lawn mower blades. It was audacious: turn a three-step operation into single-piece flow manufacturing by moving two processes together. It was a classic lean exercise to reduce waste and become more efficient.
Now the company’s senior vice president of manufacturing, Lindquist had to overcome deep debate about her idea, time studies, trial and error, and testing until the proof was in the pudding. Whirltronics went from needing to schedule and run three separate steps down to one, now completing the process with no work in progress (WIP), which decreases costs.
That first lean event — backed by upper management — proved to skeptics that cellular manufacturing could be an asset for Whirltronics. And over the years, the promise of lean has been borne out by the numbers. In 2003, blade manufacturing required six processes, 11 employees, 80-second cycle times, and 29 days of inventory. Now two decades later, the six processes require just six employees, 21-second cycle times, and two days of inventory. Whirltronics redeployed those employees into other roles that positioned the company for growth.
“It took 20 years to get there. We’re a small company but we’re tenacious and we don’t give up easily,” Lindquist says. “Continuous improvement is part of our culture and it’s an expectation with my team.”
That successful experience prompted Whirltronics to dive even deeper into its lean work. It was apparent how effective the lean efforts were, as operators started working smarter, not harder. For example, their load was literally lightened when they didn’t have to constantly move 40- to 50-pound stacks of steel blades. “I like seeing people not work as hard,” Lindquist says. “If they don’t have to lift as much and we remove the things that frustrate them and make their day easier, they have much greater job satisfaction.”
As the company grew, now to about 120 employees, Whirltronics put steady effort into lean initiatives and optimizing its workplace organization. Now all manufacturing operations are cellular, thanks to regular lean events. Each department completes a quarterly event, such as process kaizens to streamline operations and eliminate waste, or 5S events. The 5S steps of sort, straighten, shine, standardize, and sustain help Whirltronics create more organized, clean, and safe work environments, she says. In addition, Lindquist’s management team meets weekly to go over planned continuous improvement events and engage in training, developing a cohort of lean practitioners with sharp problem-solving skills.
Instead of fighting lean efforts, employees now have taken the continuous improvement ball and run with it. They submit a steady supply of idea cards for ways to make Whirltronics run more efficiently, and company leaders implement as many as they can. Operators in the packaging area originated a successful 5S event in late 2024. They designed a new layout to create room for forklift lanes, making it easier to move parts in and out of the area. The team now can run three workstations at a time instead of two, while reducing set-up time by 15%.
Employees created spaghetti diagrams, conducted timing tests, and laid out the space in an optimal way to move materials faster. “The most important thing was that they owned it, and they knew what they needed to do,” Lindquist says. “Their training was kicking in and I was so proud watching them do it. It was awesome.”Embracing lean and using it as fuel to continue innovating has
been key to Whirltronics’ 64-year longevity and consistent customer base. “We feel like Whirltronics wouldn’t be where we are today without continuous improvement,” Lindquist says. “If we hadn’t started that journey, I’m not sure where we’d be.”
AUTOMATION
Federal Package Network, Inc.
Chanhassen
To Noah Leuer, automation in manufacturing seems like a no-brainer. He has seen it make an enormous difference for Federal Package Network, the company where he is the manufacturing engineering manager. Using automation as a lean strategy hits consistent home runs, whether they reduce the number of people needed to make a product or free up time to provide more services to customers.
Operating for 45 years, Chanhassen-based Federal Package Network has two arms. Federal Package is a contract manufacturer of containers for a range of beauty and personal care products, including deodorant, lip balm, and sunscreen. FP Labs operates as a full-service skin care partner, working with beauty brands and skin care companies on research and development, product formulation, testing, and producing a host of retail-ready goods.
The company might be making a different product each week or even every day or two. This makes it imperative to have the most efficient lines embedded in its processes to keep costs down and meet customers’ requests. “We’re always looking to expand our capabilities and get better at what we do,” Leuer says. “Then we can try new things and help customers in new ways.”
A recent effort to automate Federal’s line for filling containers with deodorant dramatically decreased the number of operators from 12 to three. Now automation equipment loads the containers in the line, fills the containers with product, inserts the plug at the bottom of the container, puts them in boxes, and places them on the pallet. Cameras monitor the process to make sure everything is running smoothly. Thanks to the automation, that line doubled the units it can make per minute, Leuer says.
Automation helps everything run faster while also opening doors for employees to focus on other work. “We take these projects as a chance to move operators to more beneficial, value-adding jobs than what they were doing before,” Leuer says. “Every machine we added to that line allowed an operator to do something less repetitive. We have never gotten pushback from implementing lean. People generally have a better demeanor afterward.”
Recruiting accountable long-term employees can be a challenge for Federal, as for most manufacturers. Removing some of the day-in-day-out, tiresome work can go a long way toward holding on to Federal’s reliable workforce of 100 people. “It’s a big reason why we went the automation route,” Leuer says. “It’s not always easy. But any place we can prevent people from having to do unnecessary work is worth putting effort into.”
Already a lean practitioner, Federal hired Leuer in 2020 to bring even more attention and effort to its lean work. He quickly launched a significant automation effort for Federal’s small plastic container line — think travel size items and lip balms. It took about a year to incorporate automated filling, capping, and container loading, thanks to robotics and the new continuous motion manufacturing line. This transition occurred while Federal still operated the line at maximum capacity.
After completion, Federal could staff the line with three operators instead of seven. “There is a more repeatable process and a lot less waste than there once was,” Leuer says. “Even with fewer people seeing the line running, the process is a lot steadier, so that was a pretty successful project.”
Leuer acknowledges that automation initiatives are time-intensive, ranging from four to six months, or even up to a year for fully integrated line projects. But the return on investment comes quickly, usually within a year. For these reasons and more, Leuer champions using automation as a lean strategy.
He finds it rewarding to see his co-workers more motivated and engaged when they are doing more enjoyable and varied jobs. It’s also satisfying when company leaders can offer added capabilities and products to customers, thanks to Federal’s lean work. “To be able to create products efficiently and automatically with minimal human intervention is really neat. So is being able to hit the numbers you need to get to with automation,” Leuer adds. “We can make more products than what’s possible with human hands.”
PROCESS OPTIMIZATION
Scamp Trailers by Eveland’s, Inc.
Backus
Micah Eveland, president and CEO of Scamp Trailers, concedes that undertaking lean initiatives takes a significant investment of time, effort, and problem-solving. But as the third-generation owner of the travel trailer company, Eveland knows that the work is more than worth it.
Since Scamp started instituting a lean approach about eight years ago, the company is significantly more efficient and can build more product with fewer people. But that doesn’t mean letting some of its 72-strong workforce go. Instead, Scamp regularly pivots, adding new capabilities and service lines that will set the manufacturer up for an even brighter future, Eveland says.
“Anytime you do a continuous improvement project, there’s always a challenge, like getting buy-in from employees or working bugs out,” Eveland says. “But then things are being made more efficient for everyone, from the plant managers to the material handlers to purchasing and the line workers. It’s really neat to see the gains you get from it.”
Scamp recently completed a lean event focused on process optimization. It adopted a production tablet system that integrates with its business management software to streamline manufacturing operations. Every workstation now has an iPad that provides detailed information about each work order. That includes what inventory and tools the work requires, where they are located, what steps must be completed and when, and animated instructions — effectively a live production WIP.
The tablet arranges everything from the start date until completion, noting how many days it will take to get to the next workstation. “It keeps things flowing really nicely,” Eveland says. “If you know what you have to do tomorrow and you can mentally prepare for it, then you’re going to be more efficient when you actually get to work. Then it’s off to the races. Otherwise, you don’t know what you’re supposed to be doing, and we’re wasting so much time trying to figure that out.”
Scamp manufactures three sizes of its trailers in 17 different models, with about 40 different options — a total of 1,200 configurations. That makes it essential to know precisely what configuration teams are building so they can hit the ground running. It’s too soon to gauge exactly how much efficiency Scamp will gain from the tablet system, but Eveland projects a 25% increase.
The company has completed many lean projects over the years, focusing on foundations like workflow, organization, and automation. A recent undertaking involved forming a committee of 12 people to reorganize Scamp’s five buildings. The overall goal was to bring materials as close to line workers and stations as possible, Eveland says.
Working after-hours and on weekends to not disrupt production, the team went workshop-to-workshop to redesign whatever was necessary to eliminate wasted time. It took about six months to plan the reorganizations and a couple weeks to implement them. Some employees were frustrated that things got moved around. But they soon saw that the project made their jobs much easier, and many admitted that the changes really improved their workday.
Scamp’s culture of lean is deeply entrenched, and Eveland has the numbers to show why the focus has paid off. The company’s results from the past eight years of lean efforts illustrate its significant impact. “We’re getting more production dollars built with less labor. We’ve been gaining on that every year for the past eight years,” Eveland says. “It’s fun to look back and see that we’re making improvements, and that it’s worth it.”
Eveland has faced skepticism about lean from his employees and other manufacturing leaders, but he is convinced that it’s key to Scamp’s and other companies’ success. “I’ve seen family businesses across Minnesota and the nation that have said they don’t have time to do this or the infrastructure to do this,” he says. “If you are looking to pave the way for your company to live on for generation to generation, lean is the way to make it sustainable.”
ERROR PROOFING
TEAM Industries, Inc.
Bagley
As a key supplier to manufacturers, TEAM Industries succeeds when it sends components with no defects to its power sports, lawn and garden, and light vehicle customers. That makes error proofing a constant and critical part of its lean efforts and overall mission.
TEAM operates eight plants in the United States and Mexico that are united in its emphasis on error proofing. At its Bagley facility, employees make complete transmission assemblies. Embedded in TEAM’s processes is a regular regimen of testing and verifying its operations and products to prevent any problems from showing up at customers’ plants, says Director of Manufacturing Mike Olson.
Testing with an eye toward error proofing involves thoroughly vetting TEAM’s complex assemblies, which can have 100 components and gears that look identical to the naked eye. Employees look for issues with noise and shifting effort, while also verifying that all components are included, there are no nicks or dings in the gears, and more. “That’s part of our process to make sure nothing gets mixed up and nothing defective gets out to the customer,” Olson says.
TEAM uses a variety of ways to execute its error proofing, starting with building process quality into its manufacturing operations instead of waiting to inspect at the end of the line, says Tom Hjort, Bagley plant manager. The company uses a multipronged approach to prevent errors, including no-fault-forward technology, vision systems, and hard gauging. TEAM also regularly includes poka-yokes, a Japanese term for error proofing that identifies defects at their source and creates proactive fixes.
Error proofing is an engrained aspect of TEAM’s Process, Failure, Mode and Effects Analysis (PFMEA) system, completed by the engineering and quality group. They develop a control plan, process flow, and methods to verify that features are produced the right way, often using cameras and internal gauging. “If there’s a defect you want to catch it immediately and not make more,” Olson says. “The system won’t let you make more because you’ve mistake proofed.”
When TEAM has a new manufacturing project underway, a team including employees from product development, design engineering, quality engineering, and manufacturing engineering analyze every step of the process. Then they work to identify potential errors and their likely severity and frequency. They also assess how the team can prevent mistakes from occurring and/or quickly detect them if they do, says Ben Reiners, manufacturing engineering manager.
With these efforts, the Bagley plant now operates with the quality level of less than 50 parts per million — far below the industry standard of 300 parts per million, Hjort says. In addition, TEAM has cut internal scrap costs by 50% over the last year, according to Olson.
There are times TEAM’s Bagley plant deploys error proofing to solve problems. For example, some lines use two bearings that are exactly the same size and diameter. One is a performance bearing and one is a standard bearing, and TEAM wants to ensure that the right bearing goes in the correct spot during assembly, says Joe Frohreich, lean manufacturing engineer. The company will design a simple poka-yoke to prevent operators from putting a bearing where it doesn’t belong — making operators’ work easier and preventing mistakes.
TEAM’s commitment to lean manufacturing and error proofing means an investment of time and effort, but the company and employees can see tangible payoffs occurring constantly. Employee morale is high on the floor when things run well with minimal errors, Hjort says. And that makes everyone more willing to participate in lean-based error proofing.
“The work is relentless and ongoing, to be honest. It’s every day by everyone at every level,” Hjort adds. “But the benefit is having process control and customer satisfaction, giving customers what they want day in and day out to retain their business. It puts us on the map as the company that builds quality products and has long-term relationships with customers.”
Return to the Summer 2025 issue of Enterprise Minnesota® magazine.